Stainless steel has become one of the most commonly used materials in pump manufacturing due to its excellent corrosion resistance and mechanical properties. This article focuses on the application of several common stainless steel materials in pumps, analyzes their chemical composition differences, mechanical performance characteristics and applicable working conditions, and provides a reference for users to select models.
1. "The most familiar friend": 304 stainless steel (06Cr19Ni10)
Chemical composition and characteristics
304 stainless steel is the most commonly used austenitic stainless steel, and its typical chemical composition is:
· Chromium (Cr): 18-20%
· Nickel (Ni): 8-10.5%
· Carbon (C): ≤0.08%
· Manganese (Mn): ≤2.0%
· Silicon (Si): ≤1.0%
· Phosphorus (P): ≤0.045%
· Sulfur (S): ≤0.03%
a、Mechanical properties
·Tensile strength: ≥515 MPa
·Yield strength: ≥205 MPa
·Elongation: ≥40%
·Hardness: ≤201 HB
b、Applicable working conditions
304 stainless steel has good corrosion resistance and formability, and is suitable for:
·General corrosive media: such as dilute nitric acid, organic acids, etc.
·Temperature range: -196℃ to 800℃ (short term)
Due to the properties of 304 stainless steel, it is commonly used in: drinking water systems, food processing, and chemical industries for the transportation of weakly corrosive media.
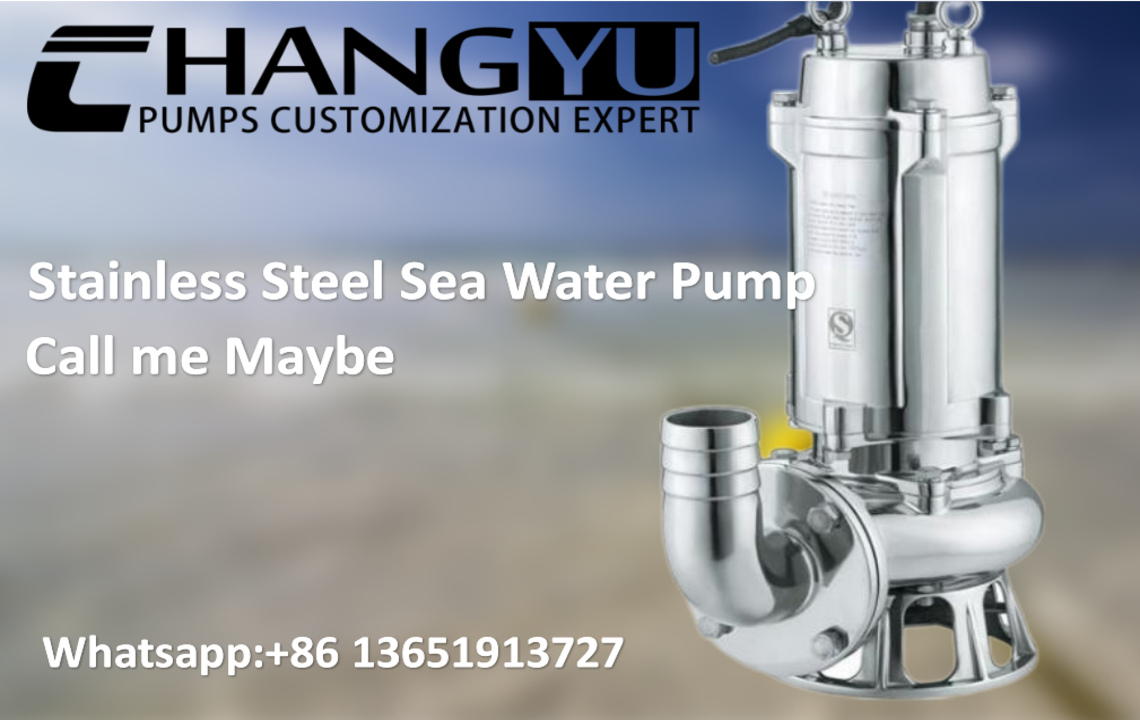
c. 304 stainless steel has limitations in use
·Not resistant to chloride corrosion (such as seawater and salt water)
·Prone to stress corrosion cracking in sulfur-containing environments
2. "A Warrior Who Rejects Corrosion": 316 Stainless Steel (06Cr17Ni12Mo2)
Chemical Composition and Characteristics
316 stainless steel is an upgraded version of 304, with the addition of molybdenum:
· Chromium (Cr): 16-18%
· Nickel (Ni): 10-14%
· Molybdenum (Mo): 2-3%
· Carbon (C): ≤0.08%
The remaining elements are similar to 304, and the corrosion resistance is greatly improved.
a、Mechanical properties
·Tensile strength: ≥515 MPa
·Yield strength: ≥205 MPa
·Elongation: ≥40%
·Hardness: ≤217 HB
b、Applicable working conditions
Compared to 304 stainless steel, 316 has better corrosion resistance due to the addition of molybdenum:
· Chloride environment: more resistant to seawater and salt water corrosion than 304
· Strong acid environment: better resistance to sulfuric acid, phosphoric acid, etc.
· Temperature range: -196℃ to 800℃ (short term)
Therefore, it is commonly used in: moderately corrosive media in seawater desalination, pharmaceutical, and chemical industries
c、Advantages
·Higher pitting equivalent PREN value (about 25, 304 is about 19)
·More resistant to crevice corrosion and stress corrosion cracking
3. "Special Forces Specialized in Solving Difficult Problems": 316L Stainless Steel (022Cr17Ni12Mo2)
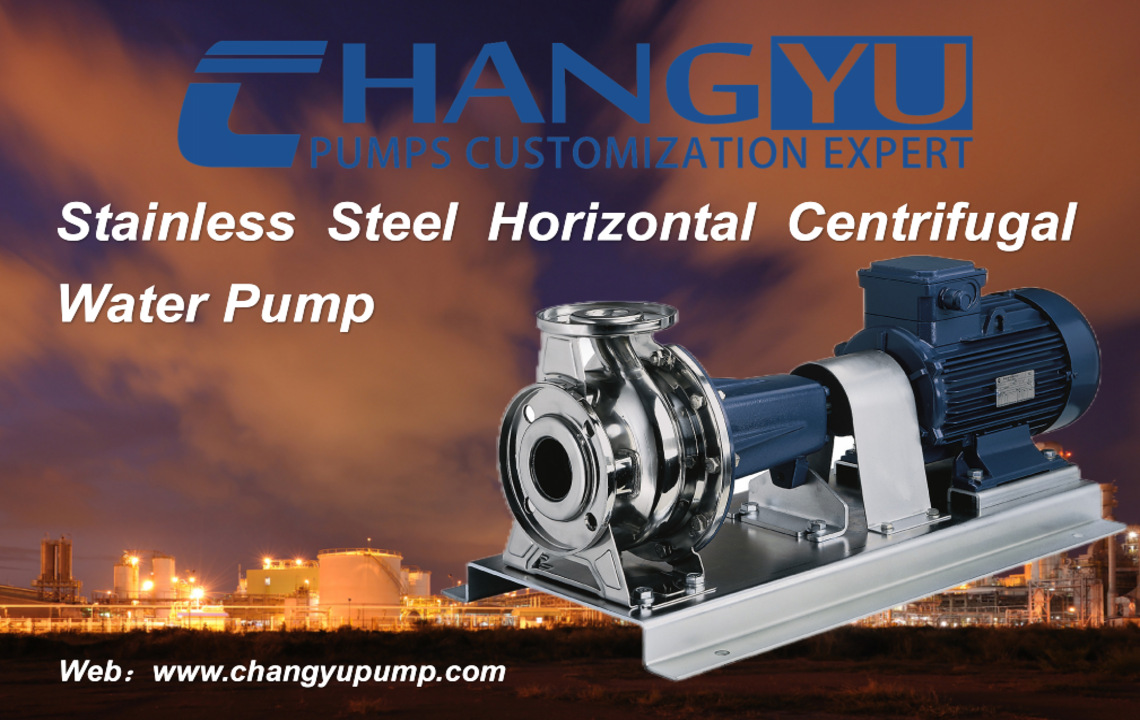
Chemical Composition and Characteristics
316L is an ultra-low carbon version of 316:
Carbon (C): ≤0.03% (significantly lower than 0.08% of 316)
The remaining components are basically the same as 316
a、Mechanical Properties
·Tensile Strength: ≥485 MPa
·Yield Strength: ≥170 MPa
·Elongation: ≥40%
·Hardness: ≤217 HB
b、Applicable Working Conditions
The low carbon content makes it more suitable for:
·Welding applications: reduce carbide precipitation in the heat affected zone of welding
·High temperature corrosion environment: more resistant to intergranular corrosion in the range of 450-850℃
·Highly corrosive media: such as concentrated nitric acid, organic acids, etc.
c、Common Applications
Nuclear industry, fine chemicals, high temperature corrosion environment
d、Special Advantages
·No annealing required after welding
·More stable in long-term high temperature environment
4. "The Smooth Socialite": Duplex Stainless Steel 2205 (022Cr23Ni5Mo3N)
Chemical Composition and Characteristics
Duplex stainless steel has both austenite and ferrite structures:
· Chromium (Cr): 22-23%
· Nickel (Ni): 4.5-6.5%
· Molybdenum (Mo): 3.0-3.5%
· Nitrogen (N): 0.14-0.20%
· Carbon (C): ≤0.03%
a、Mechanical Properties
· Tensile Strength: ≥620 MPa
· Yield Strength: ≥450 MPa (significantly higher than austenitic stainless steel)
· Elongation: ≥25%
· Hardness: ≤290 HB
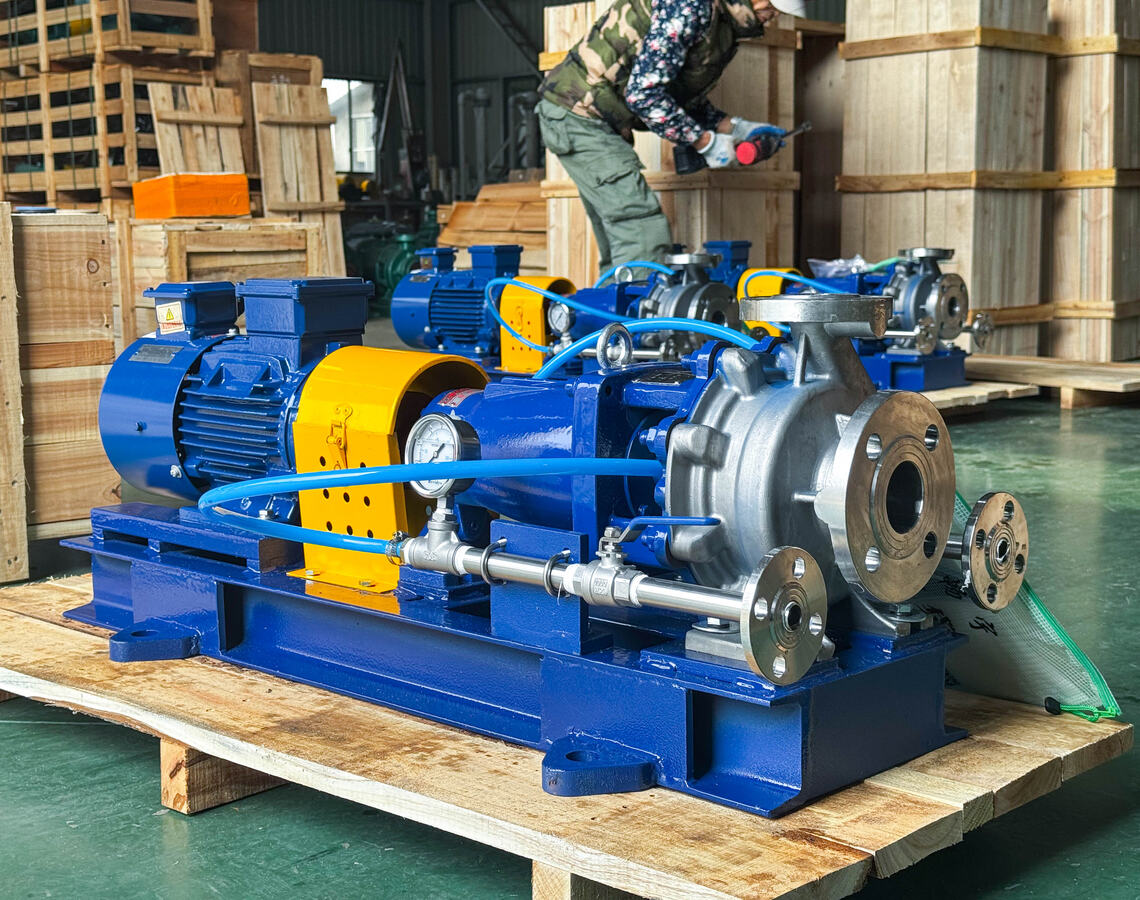
b、Applicable working conditions
2205 duplex stainless steel is particularly suitable for:
·High chloride environment: high concentration chloride solutions such as seawater and brine
·High stress environment: applications requiring high strength
·Environment where corrosion and wear coexist: such as media containing solid particles
·Temperature range: -50℃ to 300℃
·Common applications: offshore oil platforms, chemical process pumps, desulfurization systems
c、Outstanding features of 2205 duplex stainless steel
·PREN value up to 35-40
·Excellent resistance to stress corrosion cracking
·Good wear resistance and fatigue strength
5. "Challenger in extreme environments": Super austenitic stainless steel 904L (015Cr21Ni26Mo5Cu2)
Chemical composition and characteristics
Super austenitic stainless steel with high alloy content:
· Chromium (Cr): 19-23%
· Nickel (Ni): 23-28%
· Molybdenum (Mo): 4-5%
· Copper (Cu): 1-2%
· Carbon (C): ≤0.02%
a、Mechanical properties
· Tensile strength: ≥490 MPa
· Yield strength: ≥216 MPa
· Elongation: ≥35%
· Hardness: ≤220 HB
b、904L applicable working conditions
904L is suitable for extremely corrosive environments:
1. Strong acid environment: concentrated sulfuric acid, phosphoric acid, etc.
2. Complex mixed media: media containing multiple corrosive components
3. High temperature corrosive environment: up to 400℃
Because of these characteristics, 904L is commonly used in: chemical industry strong corrosive media transportation, flue gas desulfurization system, pharmaceutical industry, etc.
c、Special advantages
·Good corrosion resistance to both reducing and oxidizing media
·Excellent resistance to pitting and crevice corrosion
6. Purchase considerations
1. Medium characteristics: pH value, chloride ion content, oxidizing/reducing properties
2. Temperature range: operating temperature and fluctuation range
3. Mechanical requirements: pressure, flow rate, whether it contains solid particles
4. Economic efficiency: balance between initial cost and service life
Buyers can consult the manufacturer or make inquiries based on this information.
7. Scope of application and application recommendation
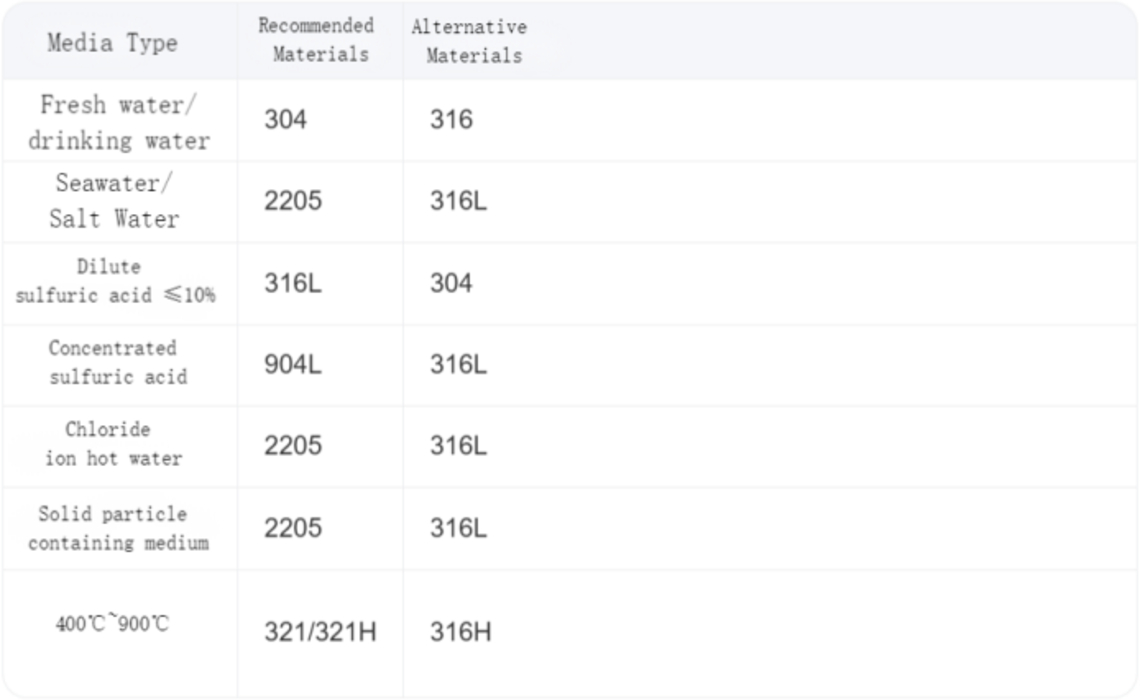
8.Conclusion
The selection of stainless steel materials for pumps requires comprehensive consideration of media characteristics, working environment and economic factors. The 304/316 series is suitable for most general corrosive environments, titanium-stabilized stainless steel is suitable for high-temperature applications, and duplex stainless steel and super austenitic stainless steel are for more demanding working conditions. The correct material selection can not only extend the service life of the stainless steel pump, but also reduce maintenance costs and ensure safe and stable operation of the system. It is recommended that users consult professional technicians when selecting and make a decision after a detailed working condition analysis.