Refrigeration System
The refrigeration system is one of the critical components of a comprehensive test chamber. Generally, refrigeration methods include mechanical refrigeration and auxiliary liquid nitrogen refrigeration. Mechanical refrigeration employs a vapor compression cycle, primarily consisting of a compressor, condenser, throttle mechanism, and evaporator. If the required low temperature reaches -55°C, single-stage refrigeration is insufficient. Therefore, Labcompanion's constant temperature and humidity chambers typically use a cascade refrigeration system. The refrigeration system is divided into two parts: the high-temperature section and the low-temperature section, each of which is a relatively independent refrigeration system. In the high-temperature section, the refrigerant evaporates and absorbs heat from the low-temperature section's refrigerant, causing it to vaporize. In the low-temperature section, the refrigerant evaporates and absorbs heat from the air inside the chamber to achieve cooling. The high-temperature and low-temperature sections are connected by an evaporative condenser, which serves as the condenser for the high-temperature section and the evaporator for the low-temperature section.
Heating System
The heating system of the test chamber is relatively simple compared to the refrigeration system. It mainly consists of high-power resistance wires. Due to the high heating rate required by the test chamber, the heating system is designed with significant power, and heaters are also installed on the chamber's base plate.
Control System
The control system is the core of the comprehensive test chamber, determining critical indicators such as heating rate and precision. Most modern test chambers use PID controllers, while a few employ a combination of PID and fuzzy control. Since the control system is primarily based on software, it generally operates without issues during use.
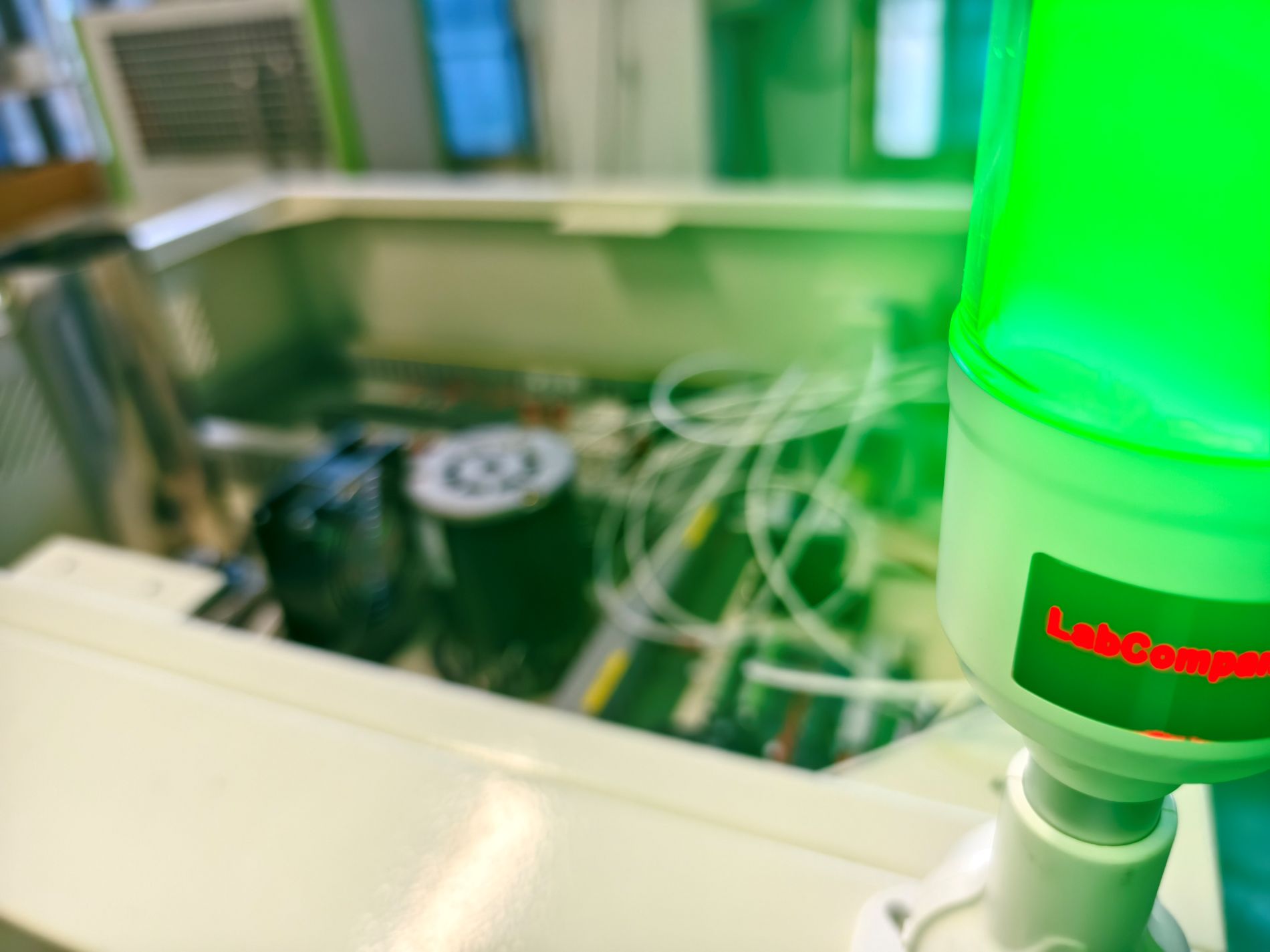
Humidity System
The humidity system is divided into two subsystems: humidification and dehumidification. Humidification is typically achieved through steam injection, where low-pressure steam is directly introduced into the test space. This method offers strong humidification capacity, rapid response, and precise control, especially during cooling processes where forced humidification is necessary.
Dehumidification can be achieved through two methods: mechanical refrigeration and desiccant dehumidification. Mechanical refrigeration dehumidification works by cooling the air below its dew point, causing excess moisture to condense and thus reducing humidity. Desiccant dehumidification involves pumping air out of the chamber, injecting dry air, and recycling the moist air through a desiccant for drying before reintroducing it into the chamber. Most comprehensive test chambers use the former method, while the latter is reserved for specialized applications requiring dew points below 0°C, albeit at a higher cost.
Sensors
Sensors primarily include temperature and humidity sensors. Platinum resistance thermometers and thermocouples are commonly used for temperature measurement. Humidity measurement methods include the dry-wet bulb thermometer and solid-state electronic sensors. Due to the lower accuracy of the dry-wet bulb method, solid-state sensors are increasingly replacing it in modern constant temperature and humidity chambers.
Air Circulation System
The air circulation system typically consists of a centrifugal fan and a motor that drives it. This system ensures the continuous circulation of air within the test chamber, maintaining uniform temperature and humidity distribution.