AEC-Q100- Failure Mechanism Based on Integrated Circuit Stress Test Certification
With the progress of automotive electronic technology, there are many complicated data management control systems in today's cars, and through many independent circuits, to transmit the required signals between each module, the system inside the car is like the "master-slave architecture" of the computer network, in the main control unit and each peripheral module, automotive electronic parts are divided into three categories. Including IC, discrete semiconductor, passive components three categories, in order to ensure that these automotive electronic components meet the highest standards of automotive anquan, the American Automotive Electronics Association (AEC, The Automotive Electronics Council is a set of standards [AEC-Q100] designed for active parts [microcontrollers and integrated circuits...] and [[AEC-Q200] designed for passive components, which specifies the product quality and reliability that must be achieved for passive parts. Aec-q100 is the vehicle reliability test standard formulated by the AEC organization, which is an important entry for 3C and IC manufacturers into the international auto factory module, and also an important technology to improve the reliability quality of Taiwan IC. In addition, the international auto factory has passed the anquan standard (ISO-26262). AEC-Q100 is the basic requirement to pass this standard.
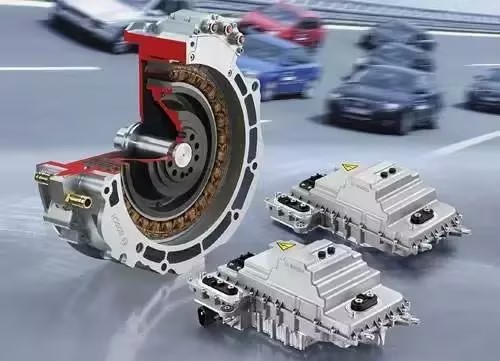
List of automotive electronic parts required to pass AECQ-100:
Automotive disposable memory, Power Supply step-down regulator, Automotive photocoupler, three-axis accelerometer sensor, video jiema device, rectifier, ambient light sensor, non-volatile ferroelectric memory, power management IC, embedded flash memory, DC/DC regulator, Vehicle gauge network communication device, LCD driver IC, Single power Supply differential Amplifier, Capacitive proximity switch Off, high brightness LED driver, asynchronous switcher, 600V IC, GPS IC, ADAS Advanced Driver Assistance System Chip, GNSS Receiver, GNSS front-end amplifier... Let's wait.
AEC-Q100 Categories and Tests:
Description: AEC-Q100 specification 7 major categories a total of 41 tests
Group A- ACCELERATED ENVIRONMENT STRESS TESTS consists of 6 tests: PC, THB, HAST, AC, UHST, TH, TC, PTC, HTSL
Group B- ACCELERATED LIFETIME SIMULATION TESTS consists of three tests: HTOL, ELFR, and EDR
PACKAGE ASSEMBLY INTEGRITY TESTS consists of 6 tests: WBS, WBP, SD, PD, SBS, LI
Group D- DIE FABRICATION RELIABILITY Test consists of 5 TESTS: EM, TDDB, HCI, NBTI, SM
The group ELECTRICAL VERIFICATION TESTS consist of 11 tests, including TEST, FG, HBM/MM, CDM, LU, ED, CHAR, GL, EMC, SC and SER
Cluster F-Defect SCREENING TESTS: 11 tests, including: PAT, SBA
The CAVITY PACKAGE INTEGRITY TESTS consist of 8 tests, including: MS, VFV, CA, GFL, DROP, LT, DS, IWV
Short description of test items:
AC: Pressure cooker
CA: constant acceleration
CDM: electrostatic discharge charged device mode
CHAR: indicates the feature description
DROP: The package falls
DS: chip shear test
ED: Electrical distribution
EDR: non-failure-prone storage durability, data retention, working life
ELFR: Early life failure rate
EM: electromigration
EMC: Electromagnetic compatibility
FG: fault level
GFL: Coarse/fine air leakage test
GL: Gate leakage caused by thermoelectric effect
HBM: indicates the human mode of electrostatic discharge
HTSL: High temperature storage life
HTOL: High temperature working life
HCL: hot carrier injection effect
IWV: Internal hygroscopic test
LI: Pin integrity
LT: Cover plate torque test
LU: Latching effect
MM: indicates the mechanical mode of electrostatic discharge
MS: Mechanical shock
NBTI: rich bias temperature instability
PAT: Process average test
PC: Preprocessing
PD: physical size
PTC: power temperature cycle
SBA: Statistical yield analysis
SBS: tin ball shearing
SC: Short circuit feature
SD: weldability
SER: Soft error rate
SM: Stress migration
TC: temperature cycle
TDDB: Time through dielectric breakdown
TEST: Function parameters before and after stress test
TH: damp and heat without bias
THB, HAST: Temperature, humidity or high accelerated stress tests with applied bias
UHST: High acceleration stress test without bias
VFV: random vibration
WBS: welding wire cutting
WBP: welding wire tension
Temperature and humidity test conditions finishing:
THB(temperature and humidity with applied bias, according to JESD22 A101) : 85℃/85%R.H./1000h/bias
HAST(High Accelerated stress test according to JESD22 A110) : 130℃/85%R.H./96h/bias, 110℃/85%R.H./264h/bias
AC pressure cooker, according to JEDS22-A102:121 ℃/100%R.H./96h
UHST High acceleration stress test without bias, according to JEDS22-A118, equipment: HAST-S) : 110℃/85%R.H./264h
TH no bias damp heat, according to JEDS22-A101, equipment: THS) : 85℃/85%R.H./1000h
TC(temperature cycle, according to JEDS22-A104, equipment: TSK, TC) :
Level 0: -50℃←→150℃/2000cycles
Level 1: -50℃←→150℃/1000cycles
Level 2: -50℃←→150℃/500cycles
Level 3: -50℃←→125℃/500cycles
Level 4: -10℃←→105℃/500cycles
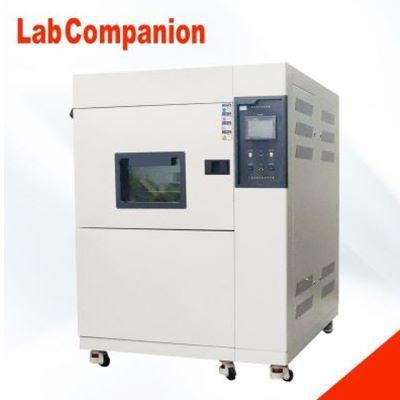
PTC(power temperature cycle, according to JEDS22-A105, equipment: TSK) :
Level 0: -40℃←→150℃/1000cycles
Level 1: -65℃←→125℃/1000cycles
Level 2 to 4: -65℃←→105℃/500cycles
HTSL(High temperature storage life, JEDS22-A103, device: OVEN) :
Plastic package parts: Grade 0:150 ℃/2000h
Grade 1:150 ℃/1000h
Grade 2 to 4:125 ℃/1000h or 150℃/5000h
Ceramic package parts: 200℃/72h
HTOL(High temperature working life, JEDS22-A108, equipment: OVEN) :
Grade 0:150 ℃/1000h
Class 1:150℃/408h or 125℃/1000h
Grade 2:125℃/408h or 105℃/1000h
Grade 3:105℃/408h or 85℃/1000h
Class 4:90℃/408h or 70℃/1000h
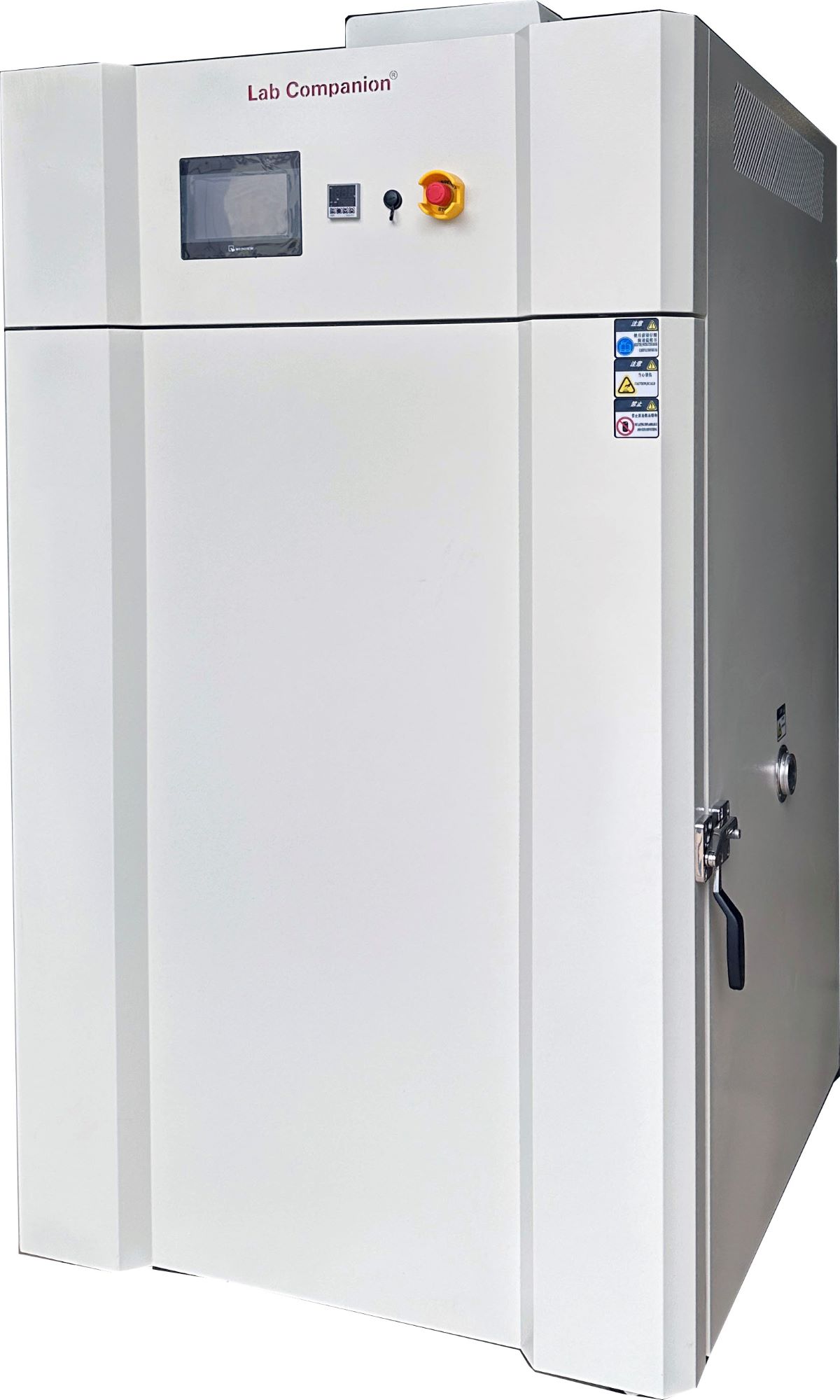
ELFR(Early Life failure Rate, AEC-Q100-008) : Devices that pass this stress test can be used for other stress tests, general data can be used, and tests before and after ELFR are performed under mild and high temperature conditions.